Dual-Fuel Power Plant EPC Project Plan I. Project Overview In response to the needs of an important South American customer, we will design and construct a power station with an installed capacity of 16MW for them. This power station needs to have the flexibility in fuel selection. In the initial stage, it will use diesel as fuel and be able to smoothly switch to natural gas in the future. At the same time, it should meet specific voltage requirements and be equipped with a soundproof enclosure, a container-type shell, and advanced control functions. II. Selection of Power Generation Equipment Engine: In view of the project's requirements for unit performance and fuel switching, a Cummins dual-fuel engine set was selected. This series of engines can operate stably in diesel mode, and after the natural gas supply is stable, it can be easily switched to natural gas mode. In order to meet the capacity demand of 16MW, it is necessary to configure multiple engine sets with suitable power, which requires a large engine power reserve and continuous work stability. The world famous brand Cummins K38-G4 engine is preferred as the basic engine. The engine power is 1220kW, and the power reserve margin is large; the engine speed is 1800rpm, which matches the unit frequency of 60Hz. The basic engine is designed and transformed into dual-fuel engine as the motivation, which maintains the efficiency of the diesel engine. The efficiency of the diesel mode is 45%, and the power efficiency of the gas mode is 42%. Generator: The Stamford generator of Cummins Company is equipped, which perfectly matches the selected engine generator set to ensure efficient power conversion. The electrical efficiency of the generator can reach 96%. The generator can be customized according to voltage requirements. For the voltage requirement of 480V/60Hz, it can be directly adapted. If the voltage output of 13.8KV/60Hz is selected, the generator will directly output this voltage level. If a 480V output is adopted, a professional step-up transformer will be configured to raise the voltage to 13.8KV for connection to the 13.8KV transmission line. Control System: It is equipped with an advanced fuel switching and flow control system, which can control different fuel supply methods and supply amounts, and quickly and smoothly switch between diesel and gas to ensure the stability and continuity of power supply. The power station is installed with a multi-unit parallel control system to realize the parallel operation of multiple engine generator sets. In addition, a remote control system is set up to facilitate operators to monitor and operate the power plant remotely and grasp the running status of the equipment in real time. Soundproofing and Container System: To reduce the impact of noise on the surrounding environment, all equipment is installed in containers with soundproofing functions. The soundproof enclosure uses high-quality soundproof materials, which can effectively reduce noise propagation and meet environmental protection requirements. The container-type design is convenient for the transportation, installation, and later maintenance of the equipment. At the same time, it provides good protection to ensure the normal operation of the equipment in various harsh environments. III. Project Implementation Steps Project Planning and Design: Utilize the professional knowledge of the company's local engineering team, combine the project requirements with the local actual situation, and conduct detailed engineering planning and design. This includes the layout design of the power plant, the design of the electrical system, the design of the fuel supply system, etc., to ensure the rationality and feasibility of the entire project. Due to the lack of on-site conditions of the customer, it is necessary to communicate closely with the customer later and adjust the design plan in a timely manner according to the customer's requirements. Equipment Procurement and Transportation: Procure high-quality equipment and materials according to the design requirements. Establish a long-term and stable cooperative relationship with suppliers to ensure the quality and delivery time of the equipment. After the equipment procurement is completed, be responsible for safely transporting all the equipment to the project site. For container-type equipment, professional transportation tools are used to ensure that the equipment is not damaged during transportation. On-site Installation and Debugging: After arriving at the project site, organize an experienced construction team to carry out the installation and debugging of the equipment. Construct strictly in accordance with relevant standards and specifications to ensure the installation quality. After the installation is completed, conduct a comprehensive debugging of the entire power generation system, including the debugging of the engine generator set, the debugging of the generator, the debugging of the control system, etc. Through debugging, ensure that the equipment can operate normally and all performance indicators meet the project requirements. Project Acceptance and Delivery: After the project debugging is completed, invite the customer to conduct project acceptance. Provide the customer with a detailed project report and equipment operation manual, and train the customer so that they can proficiently master the operation and maintenance methods of the equipment. After the customer accepts the project as qualified, officially deliver the project to the customer and provide after-sales service for a certain period to ensure the stable operation of the project.
IV. Estimation for the Dual - Fuel Power Plant EPC Project Equipment Costs: | QTY | Cummins dual-fuel generator sets vary depending on models and configurations. (Estimated based on common models, each 1000kW dual-fuel unit) | 16 units | Soundproof and container system | 16 set | Automatic transfer switch (ATS) | 16 units | Parallel control system | 16 set | Remote control system | 16 set | Project Implementation Costs: | The project planning and design costs |
| The equipment hoisting and transportation costs |
| The on - site installation and commissioning costs |
| The plant and infrastructure costs |
|
The actual price may vary due to factors such as equipment brands, specific configurations, regional differences, and market fluctuations. V. After - sales Service Equipment Maintenance: Provide regular equipment maintenance services, including equipment inspection, maintenance, and repair. Establish a professional after - sales service team and be equipped with sufficient spare parts to ensure that equipment failures can be repaired in a timely manner and downtime is reduced. Technical Support: Provide technical support to clients, answer questions encountered by clients during equipment operation and maintenance, and regularly conduct technical training for clients to improve their operation skills and maintenance levels. Equipment Upgrade: Pay attention to the development trends of industry technologies and provide equipment upgrade services to clients in a timely manner. Upgrade and transform the equipment according to client requirements and technological development trends to improve the performance and efficiency of the equipment. Through the above - mentioned plan, we are confident to provide clients with a high - quality and reliable dual - fuel power plant EPC project, meeting clients' requirements in terms of power generation capacity, fuel flexibility, voltage requirements, and finance. At the same time, we will ensure the long - term stable operation of the project with high - quality after - sales service.
Attachment 1: Product Introduction of 1000 - kW, 60 - Hz Cummins Dual - Fuel Generator Sets 1. Basic Parameters of the Unit • Rated Power: 1000kW (Diesel Mode), 800kW (Gas Mode) • Rated Frequency: 60Hz • Rated Voltage: 480V • Rated Current: 1800A • Starting Method: Started by 24V DC power • Speed Regulation Method: Electronic speed regulation 2. Engine Part • Engine Model: K38-G4 • Cylinder Arrangement: V-shaped 12 cylinders • Number of Strokes: Four-stroke • Cooling Method: Supercharged water cooling • Fuel System: Equipped with a unique low-pressure fuel pump, which can use diesel and another gaseous fuel (such as natural gas, LPG, etc.). Advanced fuel injection technologies are adopted, such as the PT fuel system with Cummins' patented technology, the high-pressure common rail fuel system, and the full-electronic control module, which can achieve ultra-high fuel injection pressure, enabling good fuel atomization and full combustion. • Intake Technology: Exhaust gas turbocharger and air-to-air intercooling technology ensure more sufficient intake air and improve the engine efficiency. • Output Power: The engine output power is generally higher than the rated power of the generator set. The output power of the K38-G4 engine can reach 1220KW (Diesel Mode) and 976KW (Gas Mode), corresponding to the rated power of the unit of 1000kW (Diesel Mode) and 800kW (Gas Mode), with a large engine power reserve margin. • Engine Power Generation Efficiency: 45% (Diesel Mode), 42% (Gas Mode).
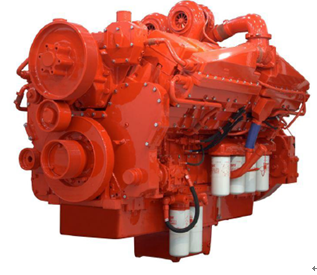
K38 Engine Parameters K38 | Type | V - type / 12 cylinders / four - stroke / four valves | Bore × Stroke (mm) | 159×159mm | Displacement (L) | 38L | Intake Method | Turbocharged and intercooled | Maximum Power (HP/kW) | 1634HP (1220kW) | Fuel System | PT fuel system | Dry Weight (kg) | 3723kg | Length × Width × Height (mm) | 2210×1320×1651 mm |
3. Performance Advantages of the Engine
Good Durability The cylinder block and cylinder head adopt a high-strength integrated design, reducing the failure rate, being durable, and having an excellent reputation. Excellent Performance The efficient Cummins exhaust gas turbocharger can ensure more sufficient intake air and improve the engine efficiency. The pressure-type pulse exhaust pipe makes full use of the waste energy, further improves the combustion, increases the engine's low-load efficiency, and reduces the engine's specific fuel consumption. It has a large torque, strong power, and a fast transient response. High Reliability Cummins' advanced PT fuel system has unique overspeed protection, low-pressure fuel supply, fewer pipelines, and a low failure rate. Originating from an excellent overall design, it has excellent reliability. Convenient Maintenance The overall modular design, block integration, compact structure, and detachable parts ensure high reusability. With the same platform design, the parts have high universality.
4. Generator Part Generator Model: STAMFORD S6L1D
• Excitation Method: Brushless self - excitation • Insulation Class: Class H • Protection Class: IP22 • Number of Phases and Wiring: Three-phase four-wire, Y-shaped. .
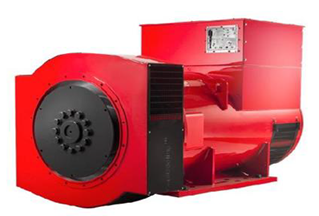
 5. Control System
• Fuel Switching and Adjustment Switch (ATS): It can quickly and stably switch between different fuel supplies or different power sources to ensure the continuity of power supply. • Parallel Control System: It can realize the parallel operation of multiple generator sets, improve the power generation efficiency and system stability, and meet the demand for greater power. • Monitoring System: The INSITE engine monitoring and diagnostic software based on the Windows operating system can monitor the running status of the generator set in real time, such as parameters like three-phase voltage, three-phase current, power, power factor, frequency, and the voltage of the control battery, and supports rapid diagnosis of engine failures. 6. Other Features
• Structural Design: The unit adopts an integrated structure. The base is made of high-strength steel materials. All the cooling fans and battery chargers are equipped with protective covers. The unit and the underframe are equipped with shock absorption devices. • Operating Environment: The general requirement for the altitude is �?/span>1000m, the ambient temperature is between -15°C and 40°C, and the relative humidity is �?/span>90%. • Application Fields: It is widely used in fields such as real estate, hotels, hospitals, schools, enterprises, mines, transportation and logistics, water conservancy and electric power, construction machinery, and construction sites, and can be used as a common power source or a backup power source.
|